Waste tire pyrolysis plant efficiently converts waste tires into valuable products such as pyrolysis oil, carbon black, steel wire, and combustible gas through the pyrolysis process. This advanced recycling technology not only addresses the growing problem of tyre pollution but also creates a highly profitable business opportunity. Moreover, with increasing global demand for eco-friendly solutions, Yushunxin waste tyre pyrolysis equipment has become an ideal choice for sustainable tyre recycling. Let’s explore more details about this powerful waste tyre recycling system.
What is the working process of waste tire pyrolysis plant?
Load Waste Tyres into the Tyre Pyrolysis Machine
Start by feeding waste tyres into the reactor of the tyre pyrolysis machine through an automatic feeder. Make sure to load only two-thirds of the reactor’s capacity to ensure smooth and efficient rotation during processing. Once the tyres are in, securely close the feeding door to begin the waste tyre to oil conversion process.
Heat the Reactor and Begin Oil-Gas Separation
Heat the reactor using available fuels such as coal, Holz., natural gas, or pyrolysis oil from the previous cycle. As the temperature reaches 100°C, oil and gas begin to form. To achieve the highest oil yield, maintain the reactor temperature between 250°C and 280°C. The system separates heavy oil gas in the manifold and channels it into a heavy oil tank after liquefaction. Meanwhile, lighter oil vapors pass through the pyrolysis oil condenser, turn into liquid, and are stored. Non-condensable gases are filtered and recycled back to the furnace for heat generation, improving fuel efficiency.
Cool the Reactor and Recover Carbon Black
After completing the oil production, allow the reactor to cool naturally. When the temperature drops by 40°C, the machine will automatically discharge carbon black into a collection system. If processing whole tyres, wait until the temperature falls below 50°C and then use a mechanical hook to extract the steel wires. This step completes the carbon black recovery process.
Reset for the Next Pyrolysis Cycle
Before starting the next batch, confirm that all materials have been removed, the reactor has cooled sufficiently, and all safety checks are complete. This preparation is crucial to maintain the long-term performance of the tyre pyrolysis plant and to ensure consistent waste tyre to oil conversion.
What is the usage of final product of waste tire pyrolysis plant?
The waste tire pyrolysis plant has become a profitable and eco-friendly solution for tyre recycling. This process not only reduces environmental pollution but also generates multiple valuable end products that can be widely applied across industries. Here is a breakdown of the four main products generated during the pyrolysis process and their respective market applications:
The pyrolysis process extracts pyrolysis oil, which contains useful compounds such as benzene, toluene, xylene, styrene, dimer pentene, trimethylbenzene, and tetramethylbenzene. These substances are commonly used as chemical raw materials in various industries.
Moreover, this oil serves as a substitute for diesel in steel plants, cement factories, boiler systems, and heavy oil generators. With further distillation, pyrolysis oil can be refined into diesel fuel, making it a high-demand energy product in both industrial and transportation sectors.
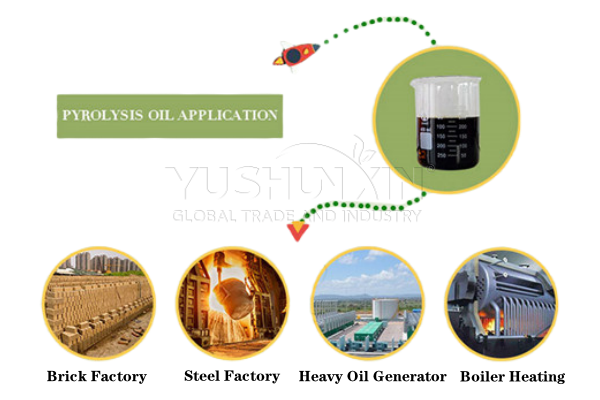
The process also produces carbon black, which is primarily used as a reinforcing filler in low-grade rubber manufacturing, including tire production and rubber soles. Ganz nachelesch, carbon black acts as a pigment for inks and paints.
In its raw form, it can be directly used as solid fuel. Wéi och ëmmer, with further milling and refining, it can be upgraded into activated carbon, opening up opportunities in filtration, purification, and chemical adsorption markets, where demand continues to grow.
Waste tyres contain embedded spring steel wire, which remains intact during pyrolysis due to the low-temperature, oxygen-free environment. This ensures that the mechanical properties of the steel are preserved.
No der Trennung, this high-quality steel can be resold to metal processing or remelting industries, offering a lucrative return and supporting the circular economy in the metallurgical field.
During pyrolysis, a significant amount of combustible gas is generated. Rather than releasing it, the plant recycles this gas as an internal fuel source for heating the reactor itself. This closed-loop system reduces operational costs and minimizes harmful emissions, improving both energy efficiency and environmental performance.
Waste tire pyrolysis plant price solution
Looking for an affordable and efficient waste tire pyrolysis plant? Whether you’re a small recycler or a large-scale investor, choosing the right capacity and price range is crucial for ROI and long-term stability.
Kapazitéit (Tons/Day) | Type | Estimated Price (USD) | Recommended For |
1-3 TPD | Batch | $30,000 – $60,000 | Small startups |
5-10 TPD | Semi-Continuous | $65,000 – $120,000 | Medium-sized plants, flexible ops |
12-20+ TPD | Fully Continuous Line | $130,000 – $300,000+ | Industrial-grade, large-scale |
Tip: Beware of overly cheap offers lacking CE/ISO certifications or proper emission control systems.
In order to further help you know the profit of waste tire pyrolysis plant, we can provide you with profit analysis of 12T/D waste tyre pyrolysis plant.
Running cost / day | |
Waste tires | 12T*73USD/T=876USD |
Heating fuel (Just choose one from the options) |
1)Coal: 0.4T*58USD/T=23USD 2)Fuel oil: 0.4T*364USD/T=146USD 3)Diesel: 0.3T*582USD/T=175USD 4)Natural gas: 150M3*0.33USD/M3=4.9USD |
Power consumption | 15Kw/h |
Water consumption | Water is for circulating use, no consumption |
Required workers | 3 workers per shift * 22USD = 65USD |
Income / Day | |
Fuel oil | 4.5T*364USD/T=1637USD |
Carbon black | 1)selling directly, 3T*73USD/T=218USD 2)grinding, 3T*291USD/T=873USD |
Steel wire | 1.5T*116USD/T=175USD |
Daily profit (Use fuel oil for heating and sell carbon black directly) |
1302USD/Day |
What more manufacturers want to know about waste tire pyrolysis plant?
About waste tire pyrolysis, you may have many other things want to know. There are some items commonly asked from our customers- waste tire recyclers for your reference. If you need more information of tire pyrolysis and machines, welcome to inquiry us immediately.
As a waste tire pyrolysis plant manufacturer with 10 years of rich experience, YUSHUNXIN not only can provide high quality waste tyre pyrolysis plant, but also can configure waste tyre pyrolysis plant according to your specific situation to help you arrange the project schedule. And if you need waste tire crushing and separating line, we can also offer for you. Contact us now for a free quote on waste tyre pyrolysis plant.
Kontaktéiert eis